TM 5-3895-367-14&P
d.
Care of Equipment in Administrative Storage.
(1)
Maintenance Services. After equipment has
been
placed
in
administrative
storage,
inspect, service, and exercise as specified
herein.
(2)
Inspection. Inspection will usually be visual
and must consist of at least a walk-around
examination of all equipment to detect any
deficiencies. Inspect equipment in open
storage weekly and equipment in covered
storage monthly. Inspect all equipment
immediately
after
any
severe
storm
or
environmental change. The following are
examples of things to look for during a visual
inspection:
(a)
Low or flat tires.
(b)
Condition of preservatives, seals, and
wraps.
(c)
Corrosion or other deterioration.
(d)
Missing or damaged parts.
(e)
Water in compartments.
(f)
Any
other
readily
recognizable
shortcomings or deficiencies.
(3)
Repair During Administrative Storage. Keep
equipment in an optimum state of readiness.
Accomplish the required services and repairs
as expeditiously as possible. Whenever
possible, perform all maintenance on-site.
(4)
Exercising.
Exercise
equipment
in
accordance with Table 4-3 and the following
instructions.
(a)
Major Exercise. Depreserve equipment
by removing only that material restricting
exercise. Remove any blocking and
perform all before-operation checks.
Operate all functional components and
perform all during and after-operation
checks.
(b)
Scheduled
Services.
Scheduled
services will
include
inspection
per
subparagraph 4-42d(2) above, and will
be conducted in accordance with Table
4-3. Lubricate in accordance with
instructions in Chapter 3, Section I.
(c)
Corrective Action. Immediately take
action
to
correct
shortcomings
and
deficiencies noted. Record inspection
and exercise results on DA Form 2404.
Record
and
report
all
maintenance
actions on DA Form 2407.
After
exercising, restore the preservation to
the
original
condition.
Replenish
lubricants used during exercising, and
note the amount on DA Form 2408.
(d) Rotation. Rotate items in accordance
with any rotational plan that will keep the
equipment in an operational condition and
reduce the maintenance effort.
e.
Procedures
for
Common
Components
and
Miscellaneous Items.
(1)
Tires. Visually inspect tires during each walk-
around inspection. This inspection includes
checking tires with a tire gage. Inflate,
repair, or replace as necessary those found to
be low, damaged, or excessively worn. Mark
inflated and repaired tires with a crayon for
checking at the next inspection.
(2)
Seals. Seals may develop leaks during
storage, or shortly thereafter. If leaking
persists, refer to the applicable maintenance
section
in
this
manual
for
corrective
maintenance procedures.
f.
Removal
of
Equipment
from
Administrative
Storage.
(1)
Activation. Prepare the equipment for normal
operation in accordance with the instructions
contained in Chapter 2, Section III.
(2)
Servicing. Resume the maintenance service
schedule in effect at the commencement of
storage, or service the equipment before the
scheduled dates in order to produce a
staggered maintenance workload.
4-43.
PREPARATION FOR SHIPMENT.
a.
The spreader should be shipped in its transport
configuration. Refer to paragraph 4-14 for instructions on
preparing the operators platform for shipment. Refer to
paragraphs 4-12 and 4-11 for instructions on installing the
transport truck and the taillights on the spreader.
b.
Reduce pressure in all tires by 10 percent before
shipping spreader.
c.
Refer to TM 55-200, TM 55-601, and TM 743-200-
1 for additional instructions on processing, storage, and
shipment of materiel.
4-73
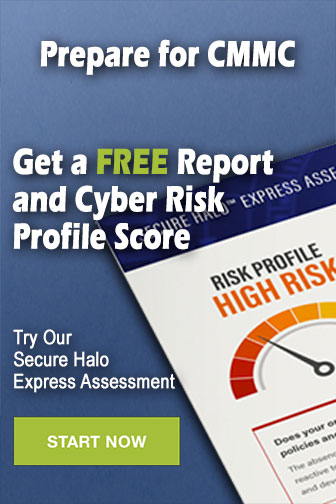